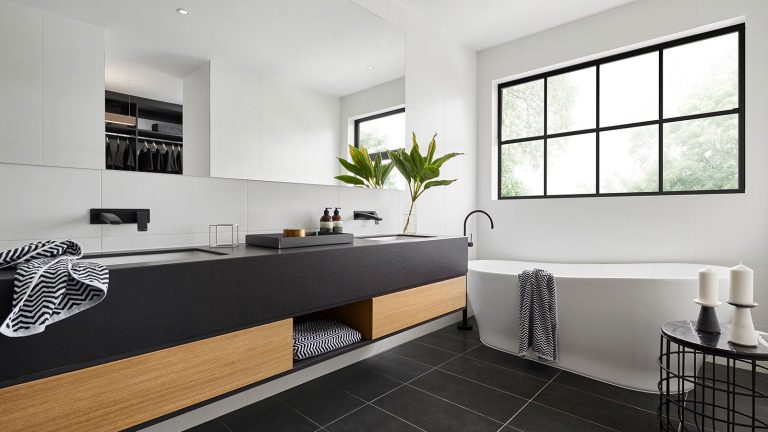
Gallery
Whenever a product has any kind of issue at any point, whether in the factory, with a supplier, or beyond the point of installation, the information is catalogued.
Over time, a wealth of data becomes available for design specialists to cross reference. The information helps the team to pinpoint opportunities for improvements, iterations, or completely new products to meet the evolving needs of builders and homeowners.
The process ensures that every effort is on the right track while the team drive forward and push to improve products.
Whether the team is looking to create a new product or improve an existing one, everything begins with brainstorming sessions.
RD&E specialists map out the issues at hand and discuss potential materials, standards or relevant regulations the team has to consider.
Once it’s all down on paper, we move to the 3D printer and prototyping. With four 3D printers in the Melbourne RD&E lab, it’s quick and efficient to develop 3D representations of new products, print early iteration models, and get a feel for how the new design will work in application.
For any one critical design issue or new product requirement, the RD&E team may prototype multiple potential solutions. At that point, it’s time to open the new concepts up to our various audiences: architects, designers, volume builders, and other key stakeholders.
The feedback sessions take place in a purpose-built pre-floor showroom. It’s a workshop environment where stakeholders can test products and the design team can record or document the results.
After the feedback is analysed and accommodated within the proposed design, we begin another variety of prototyping: developing and testing manufacture and delivery processes.
There are many ways to determine quality, depending on where the data comes from.
We collect and inspect information relating to everything from transport and logistical information through to service support, to develop a comprehensive history of the actions taking place in relation to certain jobs, projects, or customer partnerships.
All of that data is highly visible throughout the business to ensure everyone across all of our teams has ownership and responsibility for the quality of what we produce.
This approach creates an environment where every team has access to critical data that enables them to constantly refine the way they operate.
The way newly designed or redesigned products move through the production process, and whether they can be manufactured efficiently to meet a potential client’s rapid turnaround requirements.
The way new designs move through packaging and transport, to eliminate the potential for products to be impacted in ways the team could not anticipate.
The way products perform after being exposed to the real conditions of a building site, including exposure to the elements, dust, and other conditions.
For over 39 years, A&L has maintained a dedication to quality window and door designs grounded in the performance people expect, while offering the aesthetic styles they want.
The team strives to provide a carefully curated range of products to align with our varying customer needs: from luxury design features and energy efficient performance to affordable price points. Or ideally, all of these qualities at once.
From a design perspective, the innovative A&L inline reveal provides a significant performance advantage and it has done since its inception. This is true even on the standard range of products, which are incredibly cost-focused.
There is a practical advantage associated with that feature in terms of its performance and the way it looks in a home, but the inline reveal was also recognised as being much more energy-efficient, even back when there wasn’t a measurable set of criteria for energy efficiency in the way there is today.
The conventional standards and ratings used to measure energy performance in Australian homes were not in effect—they weren’t even a consideration—when the A&L inline reveal was originally designed.
The design team strives for no visible fixings and no visible drain holes, and to offer that as a standard feature across all products. This approach ensures that A&L windows sit better in application—and look better in the home—than many competing products.
In terms of standardising features to meet customers’ design requirements, some A&L windows were designed when timber windows were the predominant fashion. There are lines in our awning windows which were intended to make them look like a timber window, with all the durability benefits of aluminium. From day one, the design team at A&L have maintained a clear consideration of aesthetics.